How It Works
Liquid sludge is pumped into the DSP’s Inlet Chamber, where overflow is redirected back to the sludge source tank or process. The sludge then moves to the Flocculation Chamber, where polymer is added to aggregate or flocculate solids to create larger flocs. A slow vertical paddle mixer optimises flocculation before the sludge enters the dewatering screw.
Inside the screw assembly, a variable pitch screw moves the sludge through a series of fixed and moving rings, creating a self-cleaning, low-maintenance dewatering process. The installed gap between the fixed and moving rings varies between 0.5 to 0.1 mm, however in operation, the size of the gap sizes changes continuously for a smooth dewatering process. The filtrate passes through the gaps between the rings into a collection tray, while an adjustable pressure plate increases compression, enhancing dewatering efficiency. The filtrate can gravitate from the collection tray to the head of works or any other suitable location.
The dewatered sludge cake is discharged directly into a skip or conveyor.
Operation & Control
The Dewatering Screw Press is designed for fully automated operation, requiring minimal operator input. In AUTO mode, the system continuously monitors performance, adjusting operational parameters for optimal dewatering.
The screw motor and mixer motor are fitted with Variable Speed Drives (VSDs), allowing fine-tuning of screw rotation speed and mixer intensity to achieve the best dewatering results.
For greater flexibility, the DSP can also be operated in MANUAL mode, where each component—such as the screw, mixer, and wash system—can be individually controlled via the HMI touch screen.
Materials of construction
As standard the Dewatering Screw Press carpentry is 304 stainless steel with 316 stainless steel available as an option. The screw shaft is 316 stainless steel with a hardened 316 stainless steel replaceable edge. The rings are made of 316 stainless steel.
Key Benefits
- Single-step dewatering from as low as 0.2% dry solids to 15–20% DS cake
- High solids recovery rate of over 95%
- Compact footprint with simple installation
- Automatic and manual operation for full process control
- Low energy and water consumption
- Minimal maintenance with low noise and vibration
- Durable construction, stainless steel materials for high corrosion and abrasion resistance
- Innovative design with replaceable edge on screw shaft for easy replacement of highest wearing component
- Control panel Compliant with AS/NZS 3000
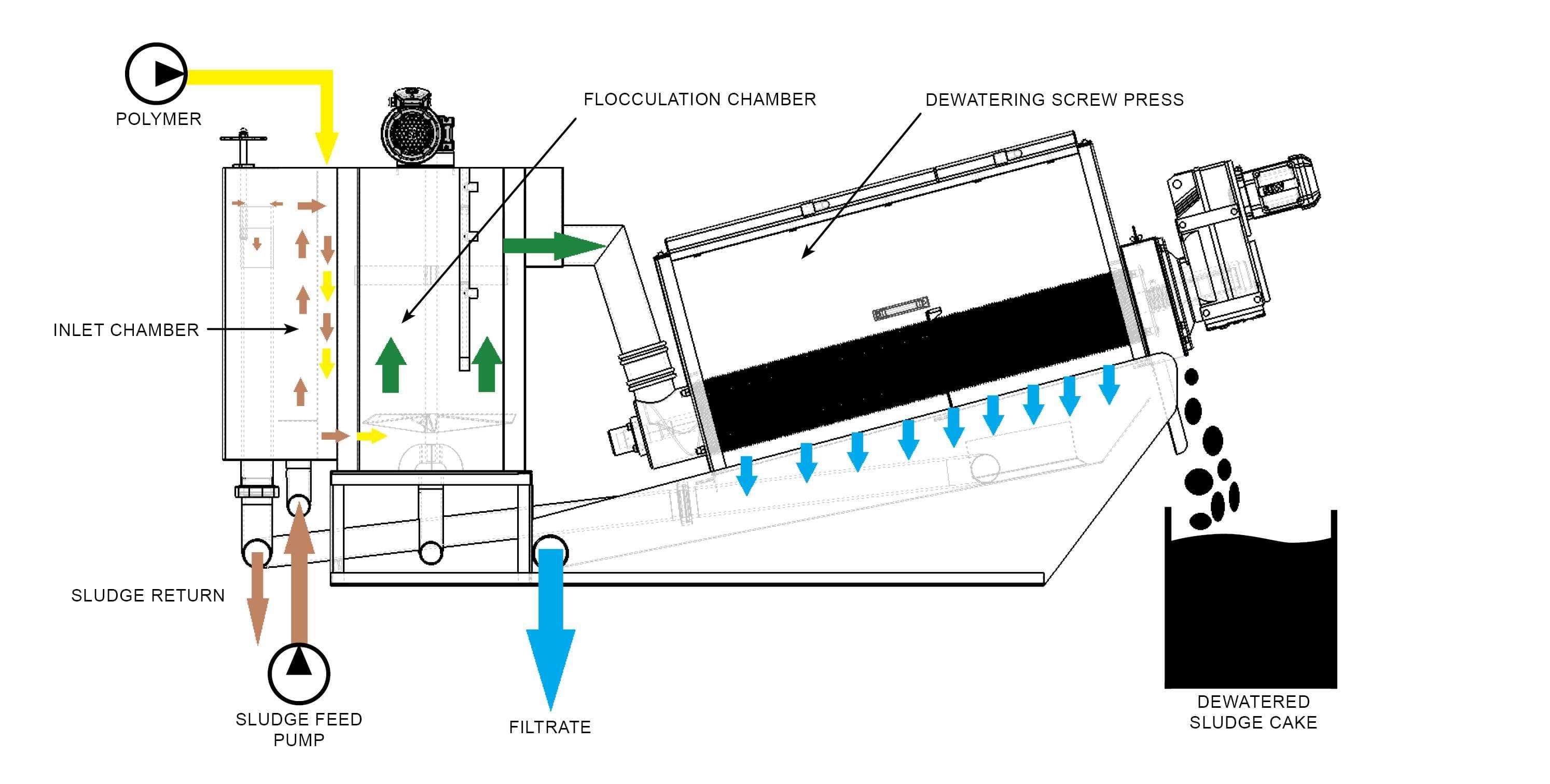
Technical Specifications
Standard Specifications
Notes:
1) Depending on specific sludge type, polymer type and polymer dose, 20% or greater additional throughput may be possible.
2) Depending on specific sludge type and polymer type, the typical polymer consumption for feed sludge concentration 2 - 5 g/L is 4-8 kg/tonne dry solids processed, and for feed sludge concentration 5 - 50 g/L is 10-25 kg/tonne dry solids processed.
3) Compressed air requirements: min 5 - max 10 bar, quality as per ISO 8573-1:2010 including particple class <5, water content <7, oil content <3
4) SEW Eurodrive (Front Transmission Gearbox)
5) Motive (Worm-Transmission Gearbox)
"F" denotes flanged connection
Standard Inclusions and Options
1 Can include Polymer Preparation System and Cake Conveyor
2 Refer to MAK Water’s Product Datasheet for Polymer Preparation System (ASP)
3 Including discharge chute between DSP and Screw Conveyor.
Disclaimer: We continuously update and improve our products and services, contact us for more detailed information or to confirm specifications. MAK Water takes no responsibility for any errors resulting from the use of information contained on this website.
Applications
Real-world examples
Sludge Handling